Complex catheters are more than just flexible tubes. They are highly engineered tools designed to navigate the body’s most delicate pathways, deliver therapy, capture images, or deploy life-saving implants. Each section, from the soft tip to the handle, has a critical job to do. Getting it right demands a precise combination of expertise, equipment, and trusted supplier partnerships.
At Medical Murray, we specialize in designing, developing, and manufacturing these advanced catheters, combining in-house capabilities with trusted partners to deliver performance, reliability, and compliance.
Critical Capabilities for Complex Catheter Manufacturers
Materials Expertise and Handling
The right materials are the foundation of every successful catheter. From Pebax and polyurethane to PTFE and nitinol, every material choice affects flexibility, pushability, kink resistance, and overall performance. Proper handling preserves these properties through the entire development and manufacturing process.
Key Focus Areas
- Temperature and humidity-controlled material storage
- Full material traceability from incoming inspection to final product
- ISO Class 7 cleanrooms for contamination-free handling and assembly
Precision Braiding, Lamination, and Assembly
Every catheter shaft combines multiple layers, often including extruded polymers, metal reinforcement, radiopaque markers, and soft distal tips. Each layer must be carefully assembled to ensure seamless performance.
Key Equipment and Capabilities
- Fine wire braiding machines for shaft reinforcement
- Thermal lamination for multi-layer construction
- Laser cutting for marker bands and hypotubes
- RF tipping, UV adhesive curing, and thermal bonding for precise component joining
- In-line vision systems for real-time dimensional verification

Seamless Component Integration
Combining soft tips, radiopaque markers, reinforcements, and functional elements like pull wires or sensors requires precise integration to maintain performance, trackability, and durability.
Key Capabilities
- Laser welding for marker bands, pull wires, and metal hypotube components
- Precision adhesive dispensing for consistent bonding
- Pull wire tensioning for steerable catheters
- Tip forming and soft tip overmolding for atraumatic transitions
Injection Molding for Tips, Handles, and More
Complex catheters require far more than long flexible shafts. Many designs call for molded components at the tip or at the handle for ideal performance and usability.
Micro Molding for Catheter Tips
Soft, atraumatic tips can be micro-molded directly onto the catheter shaft, ensuring a seamless transition between materials and a smooth distal profile.
Capabilities include overmolding soft tips onto shafts with seamless transitions.
Insert Molding for Radiopaque Markers
Radiopaque markers can be embedded directly into molded catheter tips or shaft components, ensuring secure placement without adding assembly steps.
Key Capabilities
- Precision insert molding for platinum or gold markers
- Perfect concentricity to maintain uniform profiles
Injection Molding for Catheter Handles and Hubs
A catheter is only as good as its handle, where the clinician controls torque, deflection, and delivery. Medical Murray supports the design and manufacturing of ergonomic handles that provide intuitive, precise control.
Key Capabilities
- Single-shot injection molding for handles and hubs
- Integration of metal or plastic inserts for added strength and functionality
- Textured surfaces and ergonomic shaping for enhanced clinician control
- Assembly features such as snap fits, bonding surfaces, or cable management options
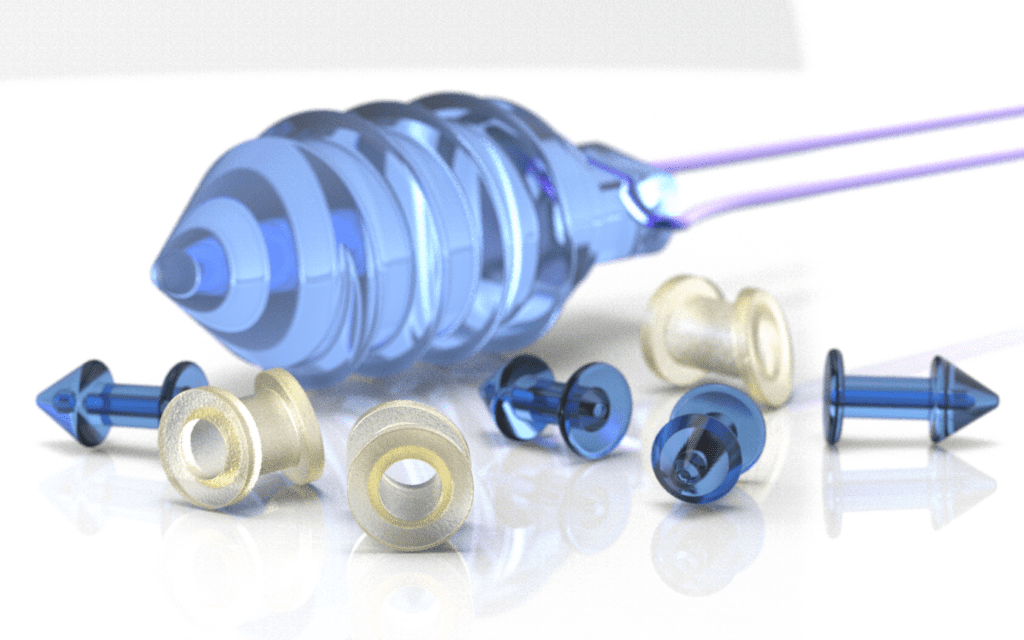
Types of Complex Catheters and Their Unique Demands
Implant Delivery Catheters
Catheters designed to deliver implants, whether a stent, valve, or occlusion device, must not only safely transport the implant but release it with controlled precision at the right moment.
Key Capabilities
- Precision implant loading and crimping
- Controlled deployment force validation
- Seamless integration of radiopaque markers for positioning under fluoroscopy
Balloon Catheters
Balloon catheters need consistent inflation and deflation performance and must reliably bond the balloon to the catheter shaft. Medical Murray partners with trusted suppliers for balloon forming while handling assembly and bonding in house.
Key Capabilities
- Balloon bonding using thermal or adhesive methods
- Inflation and deflation cycle testing to ensure reliability
- Working closely with balloon specialists for custom balloon profiles
Steerable and Deflectable Catheters
For procedures in tortuous anatomy, catheters need to respond smoothly to operator control. This requires careful integration of pull wires, torque reinforcement, and precisely tuned transitions.
Key Capabilities
- Laser cut hypotubes for enhanced torque control
- Integrated pull wire systems with balanced tension
- In-house steering and deflection performance testing
Imaging Catheters
For imaging catheters such as OCT and IVUS, clear visualization is critical. Medical Murray focuses on shaft construction and component integration while partnering with optical specialists for fiber optic splicing, imaging core preparation, and calibration.
Key Capabilities
- Precision shaft construction around pre-assembled imaging cores
- Alignment and concentricity verification to minimize rotational friction
- Partner collaboration for fiber optic splicing and optical quality testing
Ablation Catheters
Ablation catheters must deliver therapeutic energy to specific tissue targets while maintaining electrical isolation and precise temperature monitoring. Medical Murray handles catheter assembly while working with partners for specialized electrode processing.
Key Capabilities
- Electrode placement using precision bonding and welding techniques
- Electrical continuity and isolation testing to meet safety standards
- Electrode stripping and insulation processing
Comprehensive Testing and Validation
Every catheter produced at Medical Murray undergoes comprehensive mechanical, functional, and environmental testing to confirm it meets both design and regulatory requirements.
We do not just test components in isolation. Whenever possible, we simulate real world clinical use by advancing catheters through tortuous models, deploying implants, and measuring every relevant performance metric.
In-House Testing Capabilities
- Tensile and torque testing
- Navigation simulation in anatomical pathway models
- High-resolution dimensional inspection
- Pressure testing for balloons and deployment systems
- Fluoroscopy for marker positioning
- Environmental aging and thermal cycling
- Electrical continuity and isolation testing
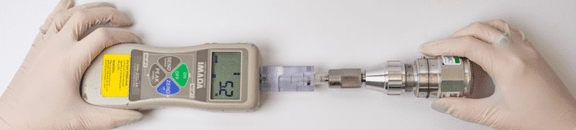
Documentation and Traceability
Every project at Medical Murray is fully documented and traceable. Our ISO 13485 certified quality management system ensures we track every material, process, and inspection from initial receipt to final product release.
Key Systems
- Electronic document control for design history file and device master record management
- ERP systems for full traceability across materials, processes, and finished devices
- Integrated quality management software to ensure continuous compliance
Combining Internal Expertise with Strategic Partnerships
Complex catheters demand more than great engineering. Success comes from combining in house expertise with strategic supplier partnerships for highly specialized processes. At Medical Murray, we have built a proven system combining advanced internal capabilities with a strong network of trusted partners. That is how we deliver high performance catheters on time and on budget.
Looking for a development and manufacturing partner who can handle your complex catheter project from design through full scale production? Contact us today!