Clinical Product
In support of clinical trials and design verification, Medical Murray conducts low-volume pilot production of devices qualified for clinical use utilizing dedicated ISO Class 7 cleanrooms, production resources, and engineering oversight. Builds are completed using released documentations and materials under our ISO 13485:2016 certified Quality Management System (QMS).
Pilot Production of clinical product at Medical Murray commonly consists of assembly, packaging, and sterilization of the product, followed by product acceptance testing to release the lot for clinical use.
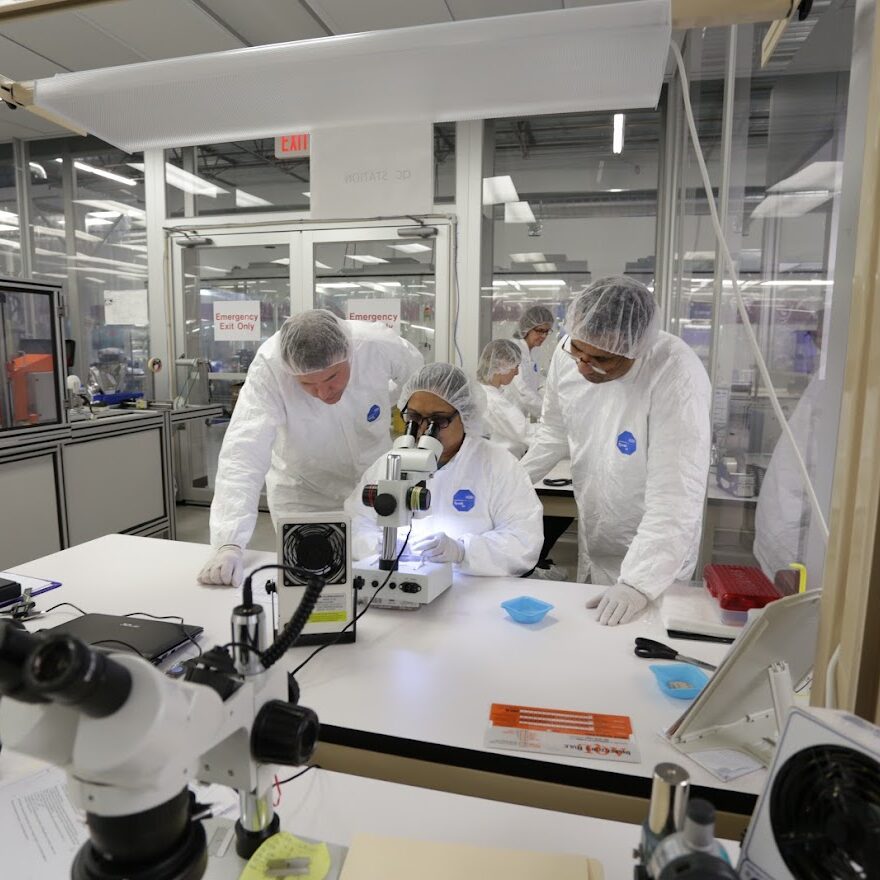
Improvements Prior to Full Scale Production
When looking for a contract manufacturer to produce your clinical product, you should choose a team that has strong base of medical device development and design experience to skillfully onboard your device.
Our engineers can provide Design for Manufacturing (DFM) and Design for Assembly (DFA) services to ensure your product is ready for pilot production. Pilot production allows our team to ensure the best possible processes are in place. Potential issues may then be identified and corrected early on before committing a significant investment in equipment, process validations, and higher quantity orders.
Based on clinical trial feedback, Medical Murray can support iterative improvements to the device followed by any necessary reverification efforts. Once the device is ready to scale, the product line can be transferred to full-scale manufacturing at either of our facilities in Lake Zurich, Illinois, or Charlotte, North Carolina.
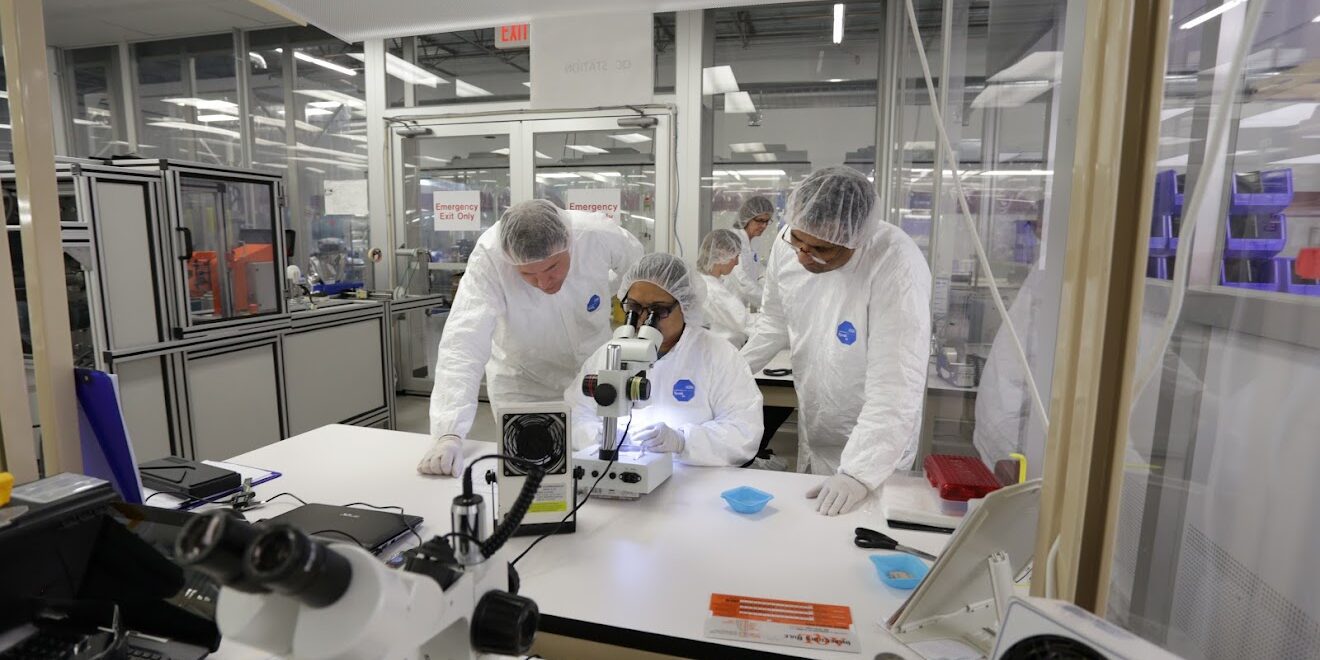
Improvements Prior to Full Scale Production
When looking for a contract manufacturer to produce your clinical product, you should choose a team that has strong base of medical device development and design experience to skillfully onboard your device.
Our engineers can provide Design for Manufacturing (DFM) and Design for Assembly (DFA) services to ensure your product is ready for pilot production. Pilot production allows our team to ensure the best possible processes are in place. Potential issues may then be identified and corrected early on before committing a significant investment in equipment, process validations, and higher quantity orders.
Based on clinical trial feedback, Medical Murray can support iterative improvements to the device followed by any necessary reverification efforts. Once the device is ready to scale, the product line can be transferred to full-scale manufacturing at our facility in Lake Zurich, Illinois.
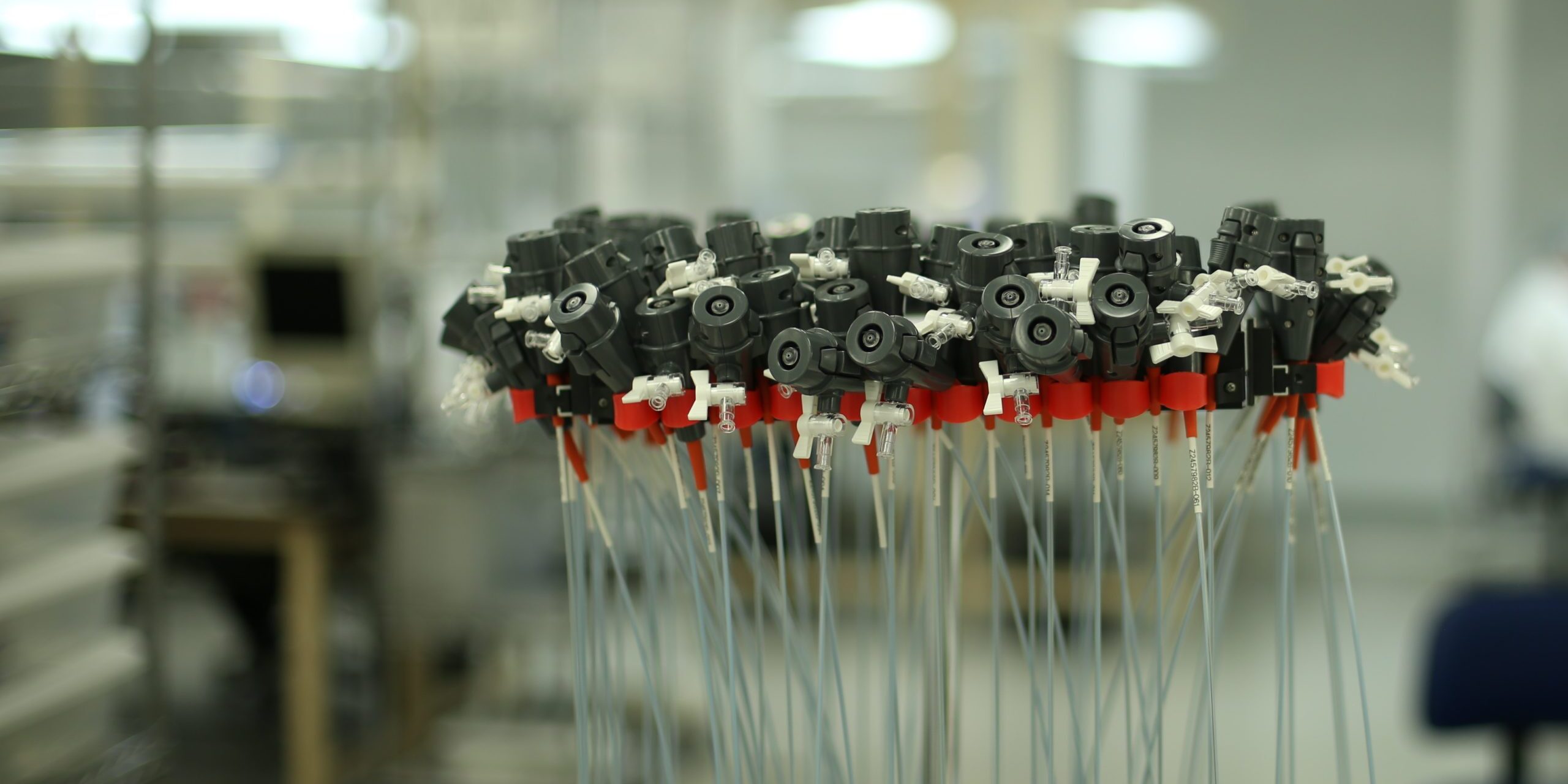
Single Lot Ordering
Medical Murray has the ability to support low-volume production orders with tight deadlines or while your product gains traction in the market. Our engineers and highly skilled technicians continue to support these critical builds, along with an experienced quality team that can support lot release testing prior to full process validations.

Lot Release Testing
Lot release testing is an integral part of quality control and ensures that your medical device design gets to market safely. Medical Murray performs product-specific testing protocols that are conducted prior to the final release of the product. This testing ensures that your medical device design functions as intended after the sterilization process is completed.
Medical Murray engineers will work in conjunction with your quality team to develop comprehensive testing protocols to qualify your product for clinical use. Lot release can be utilized for smaller builds of product that have not been through the full rigors of process validation. We offer a variety of lot release testing services, which commonly include visual & dimensional inspections and physical integrity testing.