Ever wonder how medical device engineers transform a simple wire into a lifesaving, high-tech catheter or stent? The answer often lies in Nitinol, a nickel-titanium alloy that is loved for its shape memory and superelastic properties. In other words, bend it, flex it, even tie it in knots, and Nitinol will bounce back to its original form. This post will take a closer look at why Nitinol is such a game-changer and how Medical Murray uses this remarkable material to create some of the most advanced catheters and implants on the market.
What is Nitinol?
Nitinol is a specialized alloy with many unique properties – all of which make it a perfect material for stents, reinforced catheters, and other medical devices.
- Shape Memory: Heat Nitinol above its transformation temperature, and it snaps back to a “remembered” shape. Perfect for stents that start small and expand where they need to.
- Superelasticity: Twist, bend, or stretch; Nitinol recovers without breaking a sweat. That means devices that can snake through convoluted blood vessels without kinking.
- Biocompatibility & Fatigue Resistance: Properly processed Nitinol behaves beautifully in the body and resists the repetitive stresses of daily use.
Nitinol Applications in Medical Devices
Braiding, Coiling, and Wire Wizardry
Braiding or coiling fine Nitinol wire directly onto a catheter shaft is a clever way to reinforce it without losing the necessary flexibility. Braided shafts offer impressive torque control, so surgeons can twist and turn without worrying about the device buckling. Meanwhile, coiled regions let the catheter maintain stability in some spots while staying nimble in others.

For larger devices like aortic stent grafts, Nitinol wire can be hand-fixtured onto a custom jig, then heat-set to lock in its final shape. After a short bake (usually 450–550°C for a few minutes), the alloy “remembers” the design, ensuring a targeted fit in the patient’s anatomy.
Laser-Cut Tubing, Electropolishing, and Catheter Reinforcement
Ever seen those intricate, mesh-like stent patterns? This is usually done by laser cutting. By slicing precise designs into Nitinol tubing, engineers create stents that can be crimped onto a low-profile delivery system and then self-expand once deployed. After the laser cutting, electropolishing smooths out any rough edges and rids the surface of leftover debris, which helps reduce nickel ion release and boosts device longevity.
Laser-cut Nitinol tubing isn’t just for stents, though. It can also be integrated right into the catheter shaft for added reinforcement, helping strike the ideal balance between support and flexibility.
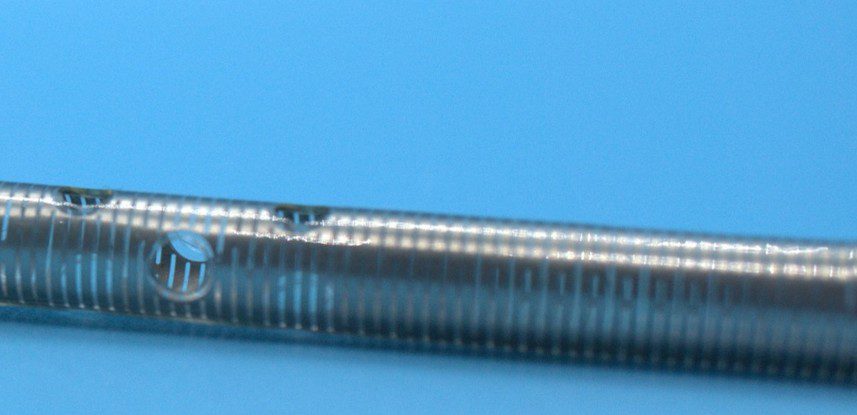
Nitinol in Medical Device Delivery Systems and Tip Deflection
Nitinol wire is often the secret sauce behind delivery systems that need repeated push-pull actions without bending out of shape. Add shape memory to the mix, and you’ve got precise locking mechanisms ready to handle anything from heart valve deployment to vascular occlusion devices.
For catheter steering, Nitinol wire is frequently welded to radiopaque marker bands at the distal tip. Clinicians can tug on the wire from the handle to deflect the catheter tip in real-time, perfect for snaking through complex blood vessels or reaching tight anatomical spaces.
How Nitinol “Remembers” its Shape with Heat
Heat setting is how we tell Nitinol to “remember” its shape. Here are the top ways we do it at Medical Murray:
- Fluidized Bed Heaters: Immersing the device in a “bed” of heated particles for quick, even transfer.
- Furnace Heat Setting: A uniform heat soak in a temperature-controlled oven.
- Electrical Current Heating: Great for shaping very localized sections by running current directly through the material.
Typical temperatures hover around 450–550°C, with dwell times of 30 seconds to 10 minutes, depending on how big or complex your device is. Some designs call for a quench in water or oil to “freeze” the microstructure, while others cool more gently in air.
Challenges of Nitinol Medical Devices and the Road Ahead
All this might sound easy, but it’s not without hurdles, like controlling transformation temperatures and perfecting welds or heat treatments. Yet, the rewards are clear: better biocompatibility, higher fatigue resistance, and the potential for even more sophisticated devices in everything from neurovascular applications to structural heart interventions.
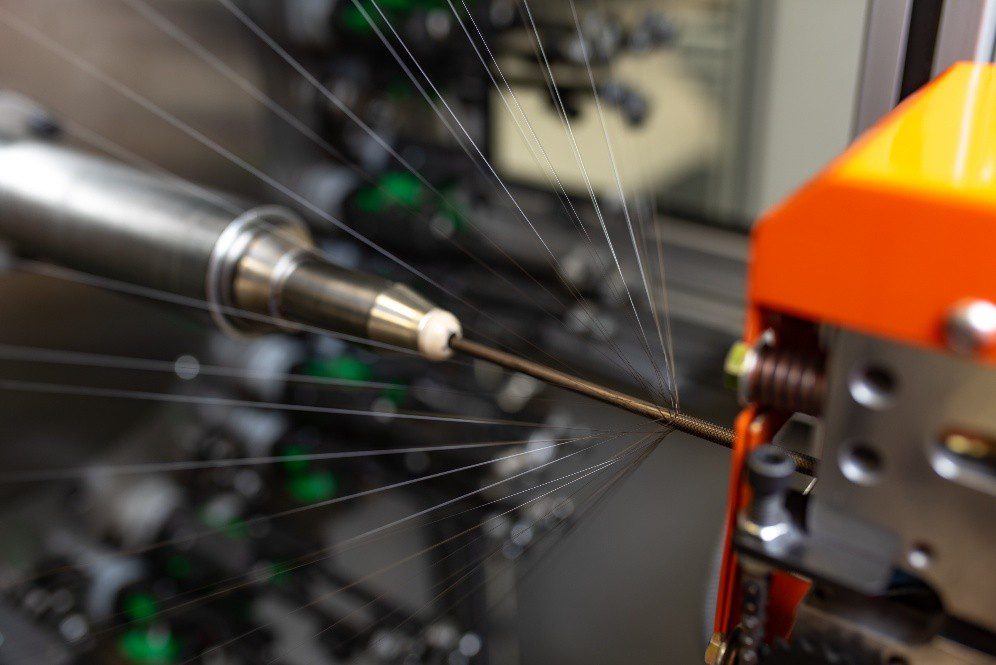
Why Medical Murray?
At Medical Murray, we specialize in turning visionary ideas into working realities, harnessing the best of Nitinol’s properties for next-gen medical devices. Whether it’s braiding wires for a robust catheter shaft, laser-cutting tubing for self-expanding stents, or hand-fixturing a large aortic stent graft, our team brings unmatched expertise to every project. It’s all part of our mission to push boundaries, tackle the toughest engineering challenges, and most importantly, improve patient lives.