Implantable medical devices are getting smaller, smarter, and more complex. Whether it’s neuromodulation implants, cardiac rhythm management (CRM) devices, or transcatheter implants and their delivery systems, precision is everything. That’s where micro insert molding is ideal for integrating miniature components into high-performance polymer implants.
This advanced manufacturing technique enables the seamless encapsulation of tiny metal, ceramic, or electronic parts within medical-grade polymers, ensuring durability, functionality, and biocompatibility. At Medical Murray, we specialize in leveraging this technology to help bring next-generation implantable devices to life.
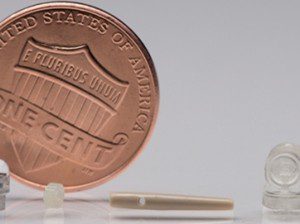
How The Micro Insert Molding Process Works
Micro insert molding is all about precision. The process involves:
- Prepping Tiny Inserts – Whether it’s microelectrodes, sensors, or reinforcement components, these inserts are treated to enhance adhesion and stability.
- Custom Mold Fabrication – High-precision tooling ensures that every insert is positioned perfectly, with ultra-fine tolerances for consistent quality.
- Polymer Selection – Materials like PEEK, TPU, LCP, silicone, and bioresorbable resins are chosen for their strength, flexibility, and biocompatibility.
- Injection Molding – A specialized machine injects polymer around the insert at controlled pressures and temperatures, encapsulating it securely without damaging sensitive components.
- Finishing & Quality Control – Post-molding processes, such as trimming, laser machining, surface treatment, and rigorous inspections, ensure top-tier performance.
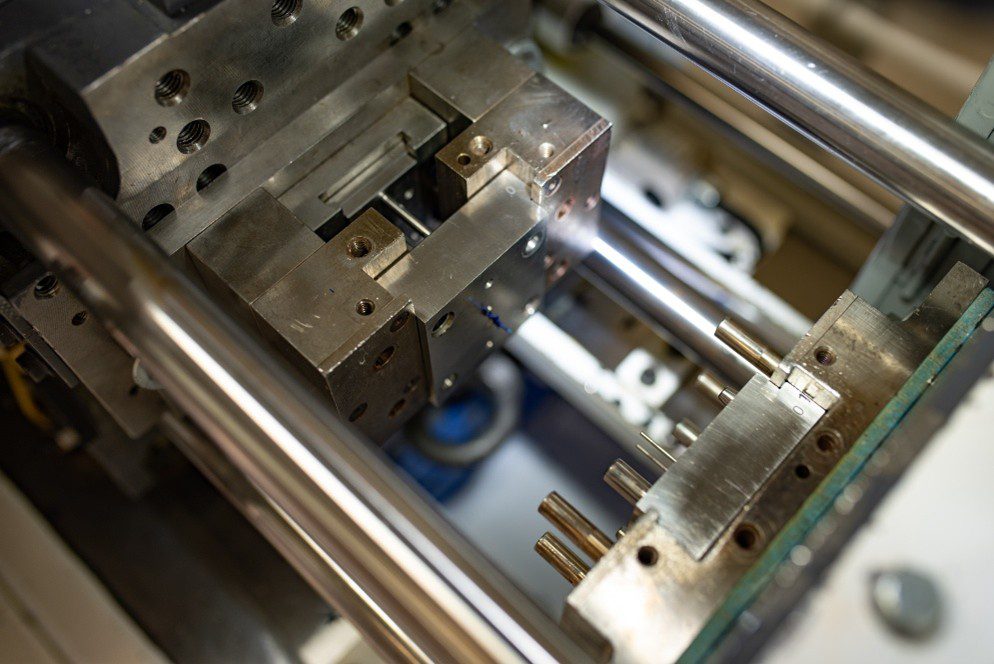
Micro Insert Molding for Neuromodulation and Cardiac Rhythm Implants
Neuromodulation and cardiac rhythm management (CRM) devices both rely on micro insert molding to ensure precision, reliability, and long-term stability in the body. These implants, such as spinal cord stimulators, deep brain stimulators, pacemakers, and defibrillators, require highly integrated components that maintain functionality under extreme conditions.
- Encapsulation of Microelectrodes and Circuits – Overmolding protects thin conductive elements and microelectronics from bodily fluids, ensuring electrical isolation and mechanical flexibility.
- Seamless Lead Integration – Insert molding secures lead-to-implant connections, preventing mechanical failure, corrosion, or disconnection over time.
- Miniaturization of Stimulation Arrays and Components – Advanced molding techniques enable smaller, more efficient implants that improve therapy effectiveness while minimizing surgical invasiveness.
- Biocompatibility and Durability – Using medical-grade materials like silicone, TPU, or PEEK, these implants remain stable inside the body for years.
- Hybrid Material Integration – Molding allows seamless bonding of metal and polymer components, enhancing the strength and performance of these life-sustaining devices.
Micro Insert Molding for Transcatheter Implant Delivery Systems
Transcatheter implant delivery systems are essential for minimally invasive procedures such as heart valve replacements, stent deployments, and other structural heart or aortic interventions. These systems require precision-molded components that ensure secure, controlled deployment of implants. Micro insert molding enhances transcatheter delivery systems in several ways:
- Securement and Release Mechanisms – Insert-molded polymer components allow controlled expansion, locking, release, and recapture of implants, ensuring precise placement within the body.
- Encapsulation of Structural Supports – High-strength polymers can be molded around metallic reinforcement elements to improve implant stability and long-term performance.
- Molded Catheter Tips for Safe Navigation – Soft yet durable materials like TPU and Pebax are molded onto catheter shafts to improve trackability and reduce the risk of vascular trauma.
- Radiopaque Features for Visibility – Integrated markers within molded components enhance fluoroscopic visibility, ensuring accurate guidance and deployment.
- Customization for Various Implant Types – Whether for self-expanding, balloon-expandable, or bioresorbable implants, micro insert molding ensures precision and consistency across all delivery components.
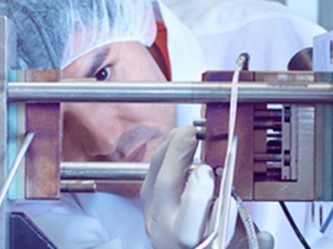
Why Choose Medical Murray for Micro Insert Molding
At Medical Murray, we bring years of experience in precision micro insert molding, specializing in Class III medical devices. Our capabilities include:
- Custom Micro Mold Fabrication – High-precision tooling for complex implant designs.
- Advanced Material Processing – Expertise in thermoplastics, elastomers, bioresorbable polymers, and composite materials.
- Regulatory Compliance – ISO 13485-certified manufacturing facilities ensuring FDA and ISO standards compliance.
- High-Precision Manufacturing – Cutting-edge micro molding technology for ultra-consistent results.
Micro insert molding supports the next generation of implantable medical devices by enabling miniaturization, enhanced durability, improved functionality, and lower cost. Whether you’re developing neuromodulation implants, cardiac rhythm management devices, or transcatheter delivery systems, precision molding is critical to success.
Want to explore how Medical Murray can support your micro insert molding needs? Contact us today.