In our previous blog post, we highlighted key trends driving innovation in interventional medical devices. As these devices become more minimally invasive, digitally connected, and complex, Medical Murray strives to deliver practical, reliable solutions that help bring the next generation of devices to life. Here’s a look at how our team is equipped to tackle today’s development challenges.
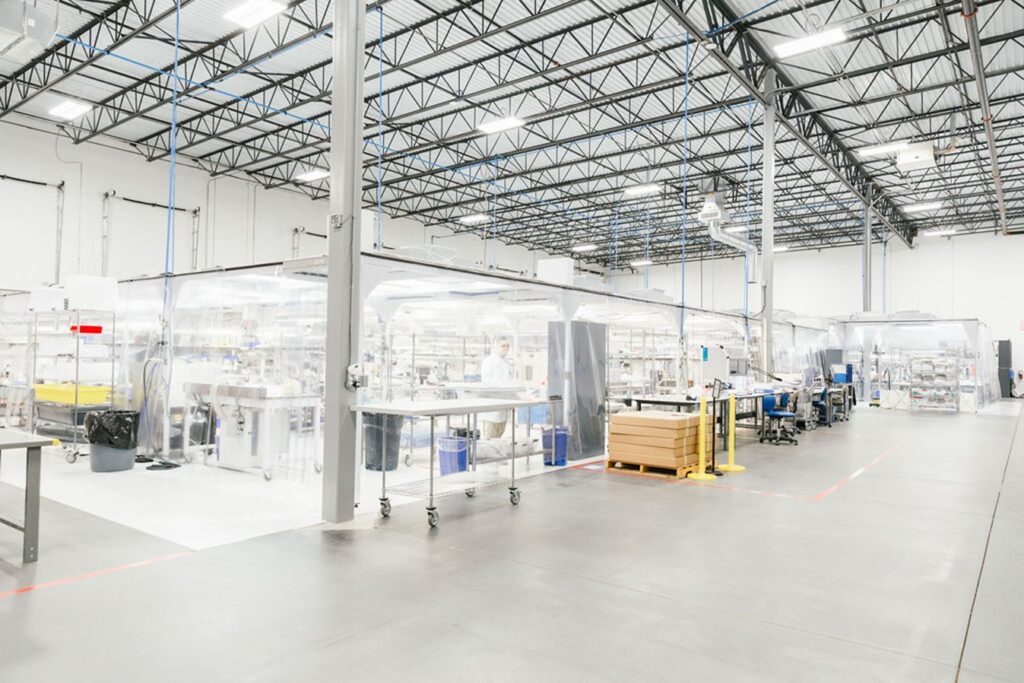
Comprehensive Catheter and Implant Development
Medical Murray specializes in designing, prototyping, and manufacturing complex catheters and implants. We work with trusted extrusion partners who excel at different sizes and materials. Our in-house expertise includes:
Braiding and Coiling Techniques
Providing structural reinforcement while maintaining the flexibility required for neurovascular, peripheral, and structural heart applications.
Medical Device Assembly and Finishing
Offering end-to-end solutions, including all secondary operations performed on the extruded tubing.
Injection Molding (Including Micro Insert Molding)
Producing precise, small-scale components that integrate seamlessly with catheters and other device assemblies.
Back-Braiding of Stents and Single-Use Catheters
Ensuring robust structural design and improved reliability across various interventional applications.
As devices get smaller and more sophisticated, strong in-house assembly capabilities—combined with flexible, high-precision molding and specialized braiding—ensure rapid design iteration and efficient scaling.
Advanced Laser Processing and Welding
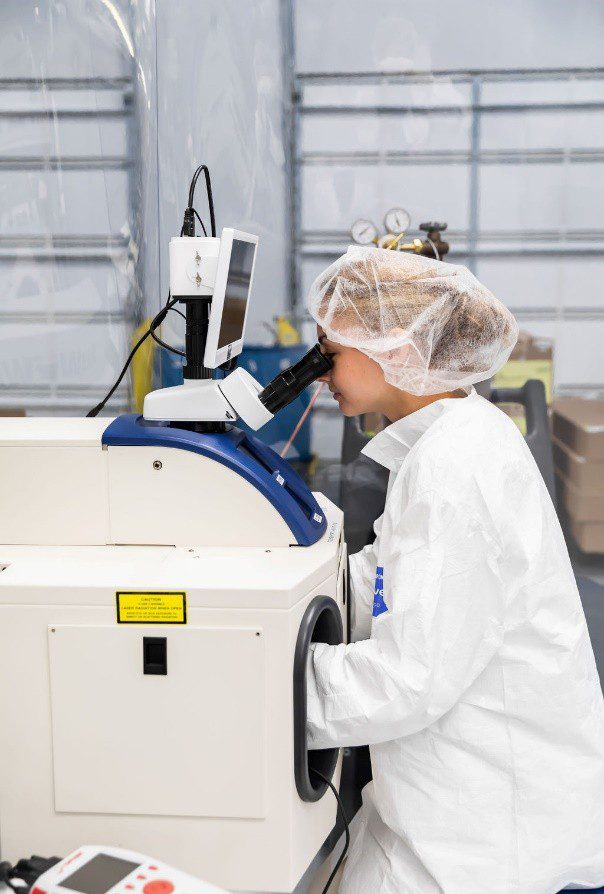
To meet demand for intricate implants and stent designs, we commonly employ fiber or femtosecond laser cutting through select partners while doing laser welding in-house for materials like stainless steel, nitinol, and specialized polymers. These processes make it possible to:
- Achieve Complex Geometry: Ideal for stent patterns and specialized device components.
- Maintain Consistency at Scale: Precision laser work reduces variability and enhances product quality.
Patients benefit from devices with finer details and better fit, while manufacturers see improved performance and reliability.
Electronics Integration and Smart Medical Devices
The industry is moving toward “smart” interventional devices—catheters and implants with integrated sensors and wireless connectivity. Medical Murray’s development team collaborates on:
- Designing Electronics-Enabled Catheters: Embedded sensors for pressure, flow, or other physiological measurements.
- Seamless Assembly in Controlled Environments: We maintain cleanrooms (ISO Class 7) to meet stringent quality standards and ensure a secure supply chain.
Incorporating electronics into interventional devices can improve real-time monitoring and data collection—key advantages for telemedicine and remote patient management.
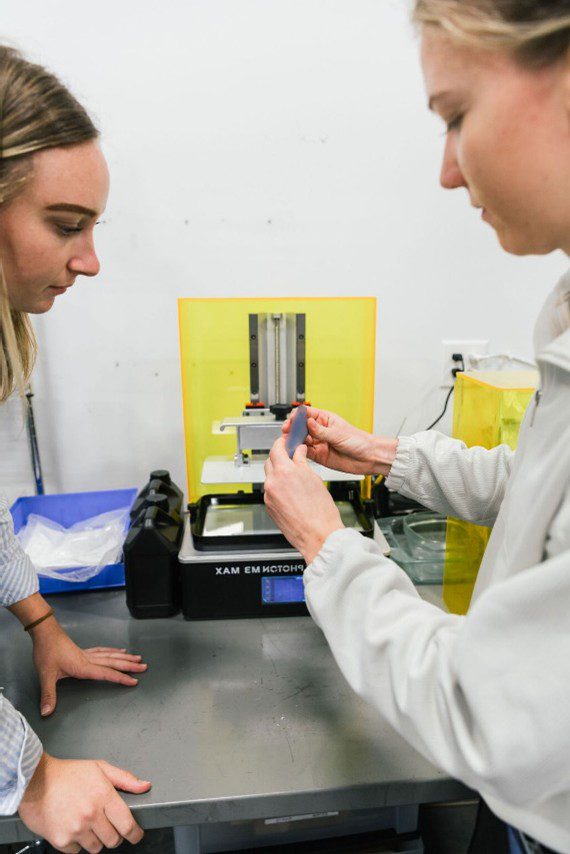
In-House 3D Printing
Medical Murray has 3D printing capabilities to expedite design verification and device assembly. We use additive manufacturing for both assembly fixtures and select medical device components, enabling:
- Rapid Prototyping: Quick design iteration saves time and reduces development costs.
- Custom Tooling and Fixtures: Tailored solutions for complex device builds.
Having in-house 3D printing capabilities accelerates R&D timelines and facilitates cost-effective small-batch production of specialized parts.
Medical Device Testing, Validation, and Regulatory Support
Our robust testing and validation services help ensure devices meet global regulatory requirements. This includes:
- Mechanical and Fatigue Testing: Simulating real-world conditions to validate strength and durability.
- Imaging and Visualization: Verifying deployment, navigability, and performance in anatomically relevant models.
By identifying potential issues early, we help accelerate regulatory approvals, limit costly redesigns, and enhance patient safety.
Ongoing Innovation: Our Advanced Development Group
Beyond current capabilities, Medical Murray maintains an Advanced Development Group (ADG) dedicated to exploring and evaluating emerging technologies, such as:
- Novel Materials Research: Studying biocompatible polymers, biodegradable structures, and shape-memory alloys.
- Next-Generation Sensor Integration: Pursuing early-stage work on microelectronics, wireless power, and AI-driven data analysis.
- New Process Adoption and Automation: Welcoming innovative methodologies while automating existing processes to boost quality and efficiency.
This forward-thinking approach ensures we continually refine and expand our capabilities, readying ourselves—and our clients—for the next wave of medtech innovation.

Staying on Top of Medical Device Industry Trends
As interventional devices become more sophisticated and patient-focused, manufacturers need a partner that offers integrated development, manufacturing, and regulatory support—backed by both strong partnerships and in-house skills. Medical Murray is committed to evolving our expertise and infrastructure in lockstep with market demands, and our Advanced Development Group stands at the forefront—helping us anticipate and invest in the capabilities that matter most.