When it comes to manufacturing complex medical devices like catheters and transcatheter implants, selecting the right pathway can make all the difference. Should you work with a CDMO to develop your device and transfer it into manufacturing? Or is your device already developed and ready for a manufacturing line transfer? Do you start with pilot production or move straight to full-scale manufacturing?
These are big decisions that impact timelines, costs, and long-term success in medical device manufacturing. At Medical Murray, we specialize in helping companies navigate these choices with confidence, and this guide will help you ask the right questions and find the best fit for your device.
“Development and Transfer” vs. “Manufacturing Line Transfer”
Your first decision depends on your device’s status and the support you need to bring it to market.
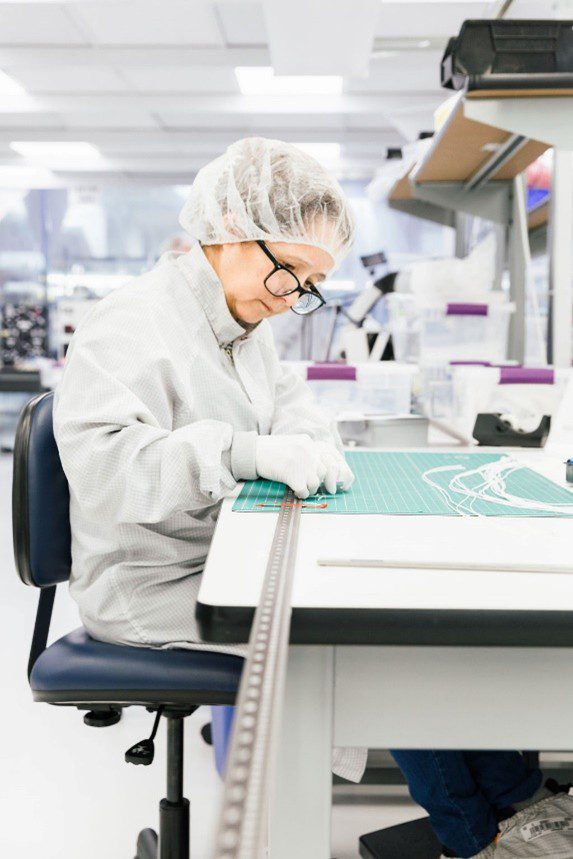
Questions to Ask:
- What is the current stage of your device?
If your design is evolving or needs optimization, development and transfer is the best path.
If your design and manufacturing processes are fully validated, a manufacturing line transfer might make sense.
- Do you need help with materials, suppliers, or processes?
If yes, development and transfer can ensure these are optimized for manufacturability and compliance.
If no, manufacturing line transfer can focus on replicating existing validated processes.
- Are inspection protocols in place?
If not, development and transfer offers the opportunity to build inspection steps tailored to your device.
If yes, make sure your CDMO can replicate and validate your inspection methods during a line transfer.
Key Takeaways
- Development and Transfer is ideal for devices requiring design adjustments, custom manufacturing process development, or enhanced inspection protocols.
- Manufacturing Line Transfer works best for fully developed devices with established processes and established quality systems.
For catheters and transcatheter implants, this decision is critical. Devices with complex features often benefit from a development and transfer process that ensures every element is optimized before scaling up.
Pilot Production vs. Full-Scale Manufacturing
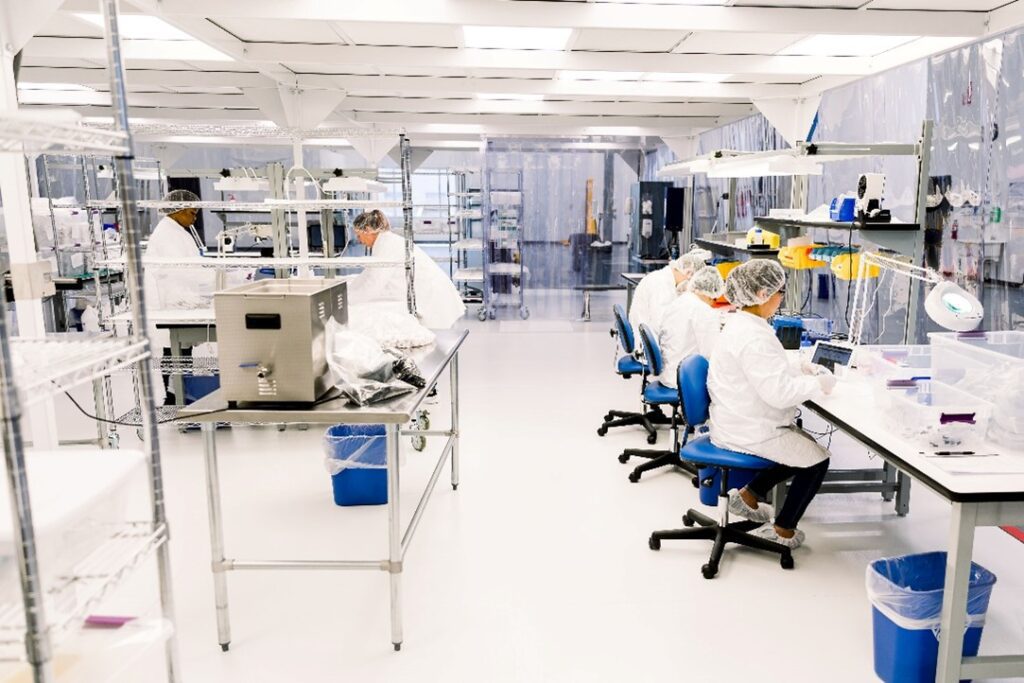
Once your device is ready for manufacturing, the next question is whether to start with pilot production or jump into full-scale manufacturing.
Questions to Ask:
- What is the purpose of this production run?
If you need small batches for clinical trials, design validation, or early market entry, pilot production is the way to go.
If you’re ready for sustained commercial distribution, full-scale manufacturing is the better fit.
- What volume do you need?
Small batches for testing or early distribution align with pilot production.
High-volume, continuous production requires the efficiency of full-scale manufacturing.
- Are your processes and inspections validated?
If not, pilot production allows for iterative refinements and single-lot release or partial validations.
If yes, full-scale manufacturing ensures stable, high-throughput operations with established quality controls.
Key Takeaways:
- Pilot Production is perfect for early-stage production runs that require flexibility and intensive inspection.
- Full-Scale Manufacturing provides the efficiency and scalability needed for long-term commercial success.
For devices like catheters or implants, pilot production often involves testing specialized features such as nitinol-based assemblies or complex custom protocols. Full-scale manufacturing, on the other hand, focuses on maintaining these features while increasing production efficiency.
Choosing the Right Contract Manufacturing Partner
The medical device contract manufacturing partner you choose will significantly influence the success of your manufacturing journey. Here’s what to consider:
- Experience with Your Device Type: Does the manufacturer have expertise in manufacturing complex catheters, implants, or other interventional devices?
- Inspection and Validation Capabilities: Can they handle advanced inspection systems, like vision-based inspections, and meet regulatory requirements?
- Scalability: Do they have the capacity to transition seamlessly from pilot production to full-scale manufacturing?
- Integrated Services: A manufacturer that offers packaging, sterilization management, and regulatory support simplifies the process and reduces risk.
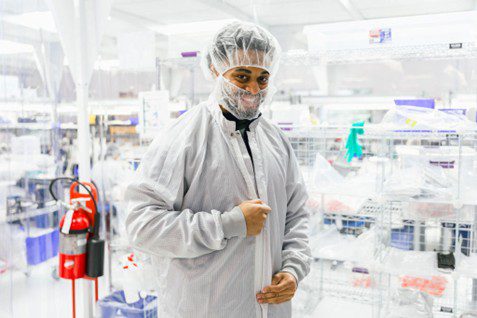
Ready to Get Started?
At Medical Murray, we specialize in the development and manufacturing of complex interventional devices, including catheters and transcatheter implants. Whether you’re navigating development and transfer, manufacturing line transfer, pilot production, or full-scale manufacturing, we have the expertise to guide you every step of the way.
Need help deciding on the right path for your device? Contact us today to learn more about how we can support your project.
Medical Murray is a leading CDMO specializing in complex catheters, transcatheter implants, and other interventional devices. We are committed to quality, compliance, and innovation in every stage of the medical device lifecycle.