The world of catheter innovation is advancing rapidly. With the growing complexity of medical procedures, the demand for catheters with advanced functionalities continues to rise. Unlike simple, well-established catheter designs, complex catheter manufacturing faces unique challenges in design, materials, and production.
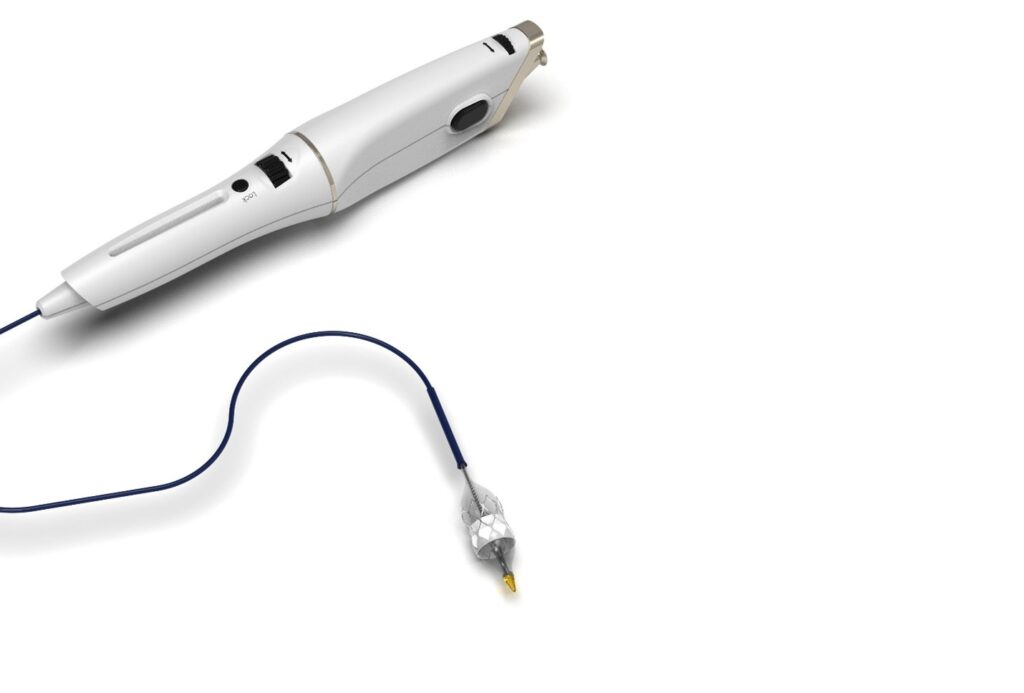
What Makes Complex Catheter Manufacturing Difficult?
There are a few distinct challenges that make manufacturing complex catheters more difficult than other designs.
Design Complexity
Simple Catheters: Design limited to a few features, commonly single-lumen or co-axial shaft, straightforward manufacturing and predictable performance.
Complex Catheters: Features a combination of complex features, multi-lumen, reinforced shaft, integrated sensors, steerable tips, balloons, and other advanced components. These designs require innovative engineering and precision.
Material and Manufacturing Challenges
Simple Catheters: Use standard materials like polyurethane or nylon with well-established extrusion and molding techniques.
Complex Catheters: Require specialized materials such as nitinol, radiopaque markers, fluoropolymers, multiple durometers, electrodes, sensors, balloons, flexible imaging fibers, etc. Advanced manufacturing processes like laser machining, over molding, and high-precision bonding are often necessary.
Regulatory Demands
Simple Catheters: Commonly Class II devices with moderate regulatory requirements.
Complex Catheters: May be Class III, requiring extensive design history documentation, verification, and validation to meet regulatory standards for FDA and/or MDR.
Real-World Examples of Complex Catheters
Transcatheter Implant Delivery Systems
Transcatheter implant delivery systems are built to place life-saving devices like heart valves, stents, and other implants with precision. They use steerable tips and high-strength materials to navigate challenging anatomy.
Some systems rely on balloons for expandable implants, ensuring controlled inflation for accurate placement. Others handle nitinol self-expanding implants, offering controlled release and re-capture for repositioning or retrieval.
Imaging Catheters

Imaging catheters are essential tools for real-time visualization of blood vessels, commonly used in procedures such as intravascular ultrasound (IVUS) and optical coherence tomography (OCT).
These catheters integrate advanced imaging fibers or high-resolution sensors into their design, enabling clinicians to assess vessel structure, measure plaque buildup, and guide interventions with precision.
Robotic-Assisted Catheters and Single-Use Scopes
Robotic-Assisted Catheters: Designed for navigation with robotic surgical systems, these catheters often use laser-cut tubes for high maneuverability and structural integrity, allowing the most accurate articulation in complex procedures.
Single-Use Scopes: Feature high-resolution, cost-effective cameras and micro-cables for real-time imaging, integrated into handles requiring micro-soldering assembly operations.
Electrophysiology Catheters
Electrophysiology catheters are used to diagnose and treat arrhythmias by mapping electrical activity in the heart and, in the case of ablation catheters, delivering energy to targeted areas for therapy.
These devices feature multi-electrode arrays that demand precise insulation, signal accuracy, and thermal management to ensure safety and effectiveness in delicate cardiac procedures.
Strategic Tips for Phasing Development
Phase 1: Concept and Feasibility
- Focus on initial prototypes to identify technical risks.
- Evaluate the feasibility of manufacturing methods and regulatory requirements early.
Phase 2: Iterative Design and Testing
- Refine the design based on early testing and feedback.
- Develop processes alongside design refinement to ensure scalability.
Phase 3: Design for Manufacturing (DFM) and Process Validation
- Transition prototypes into manufacturable designs, finalizing tooling and process flows.
- Perform full design verification using production-ready units to reduce the need for rework.
Phase 4: Clinical Trials and Commercialization
- Conduct clinical trials with devices produced from validated manufacturing processes.
- Ensure that the design and processes are scalable for commercial production goals.
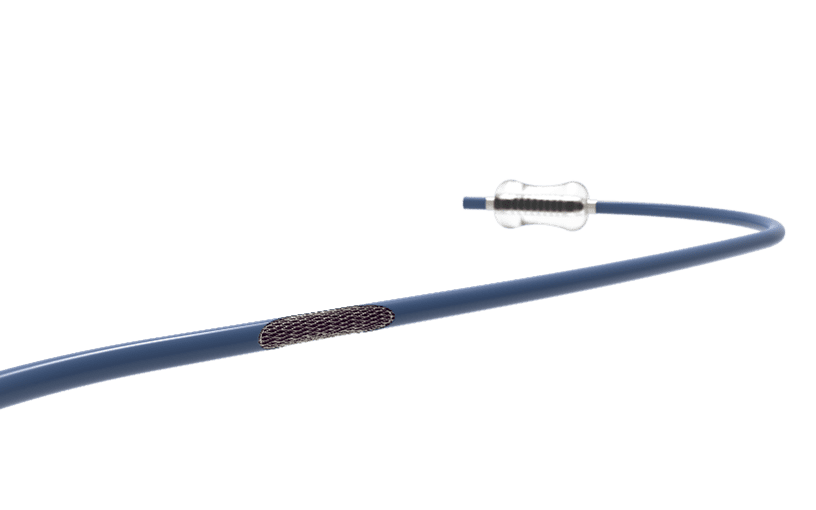
Balancing Clinical Results with Contract Manufacturing Readiness
Fast-Tracking Clinical Results
- Pros: Accelerates clinical validation, attracting investors or early approval.
- Cons: May require repeating design verification and clinical trials if significant changes are needed post-testing.
Prioritizing DFM and Process Development
- Pros: Reduces risk of delays, cost overruns, and regulatory setbacks.
- Cons: Extends the timeline for reaching initial clinical trials.
Catheter Contract Manufacturing that Balances Function with Scalability
For Class III medical devices, prioritize simultaneous design refinement and process development during Phase 2. This ensures that clinical trials use production-ready designs, minimizing the risk of repeating design verification or clinical trials.
Developing complex catheters like transcatheter implant delivery systems, imaging catheters, robotic-assisted devices, and electrophysiology catheters requires a strategic approach to overcome technical, regulatory, and manufacturing challenges. With thoughtful planning and phased development, you can balance clinical readiness with manufacturability to bring innovative solutions to market.
Need help tackling the complexities of catheter development? Contact us. We specialize in bringing cutting-edge medical devices to life. Let’s talk about how we can support your project.