Processes and tooling methods for successful bonding and shaping of complex catheters for minimally invasive procedures.
Authored by: Andrew Black & Tanner Hargens
The physical shape and size of both a catheter shaft and tip plays a significant role in the overall success of an operative procedure, and in minimizing trauma and recovery time in the hospital. Catheters support a host of interventional treatments ranging from endotracheal to intra-vascular procedures. Examples of catheter use include measurement of blood pressure or flow, fluid drainage, drug delivery, surgical instrument access, and implant placement. These procedures can often be accomplished with minimally invasive surgical techniques resulting in smaller incisions and faster procedures.
Why Catheter Tips Are Needed
Catheters offer a great benefit in allowing access to locations within the body that are difficult to reach via conventional surgical methods. To reach its target destination, a catheter must often pass through the complicated geometry of a vessel within the body, without causing harm. This can be especially challenging for cardiac catheters where the tubing must be stiff enough to allow control of the catheter as it advances through the body, yet the leading tip must be flexible enough to maneuver into smaller blood vessels without causing trauma to the surrounding tissue.
In order for the device to have such contradictory features, it is common for the catheter to be made of different materials throughout its length. Catheter shafts are typically made of materials with relatively high modulus of elasticity strength to provide the ability to push, torque, and turn inside the body cavity. A catheter tip may require a different material or shape than the catheter shaft to function properly and aid patient comfort by reducing pain, leakage, and tearing of the tissue.
The distal tip will often have a reduced modulus for greater flexibility and a reduced profile or tapered shape to pass smoothly through the anatomy. The shape and taper length of the tip is often a key design feature to allow for the advancement of the catheter within challenging anatomy. Due to the rapid growth of minimally invasive surgical procedures utilizing catheter devices, the demand for this type of custom catheter tip has become prevalent.
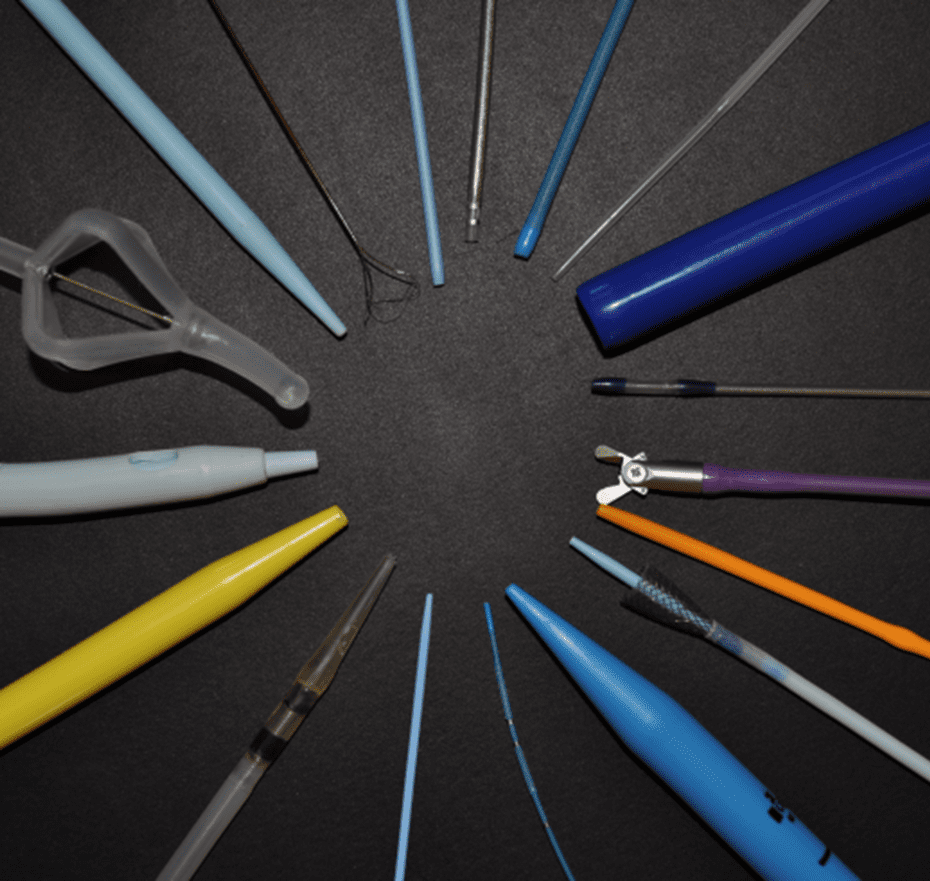
Materials Overview & Tooling Methods
Different extrusions can be joined by adhesives or a combination of pressure and heat generated from hot-air or radio-frequency. Catheter tips can be formed, tapered or sealed by similar melt processing techniques. The bonding or shaping must be done in a way that leaves a seamless exterior and a seamless interior to allow easy passage of components such as guide wires, needles, and other catheters.
There are many types of polymer materials available for flexible catheter extrusions and tips ranging from thermoset silicone to thermoplastic polyethylene; however, thermoplastic polyurethane is the most widely used. Polyether-based polyurethanes are able to achieve a broad range of physical and mechanical properties and they are easy to process, often allowing the catheter shaft and the distal tip to be from the same polyurethane material but with different moduli to match the performance requirements of the catheter.
When producing first prototypes of a catheter concept from thermoplastic polyurethane, a simple and economical method involves hot air and heat shrink tubing. For a simple butt joint, a PTFE coated mandrel or PTFE beading is inserted into the lumens that are desired to be left open.
Polyester heat shrink tubing is positioned over the joint before compressing the extrusions together under hot air. Once the joint has cooled, the heat shrink and mandrel can be removed. When done properly, the joint will be smooth and strong enough to ensure the two different materials do not separate during their intended use.
A similar method can also reshape the profile of a tip. A polyester heat shrink segment is placed over the extrusion tip and exposed to heat. While heating, tension is applied to the heat shrink as it compresses the extrusion into a softer conical tip shape with a reduced diameter.
The process to produce first prototypes should begin the transfer to a more production-friendly process once the design has been verified as functional or a processing limitation has been met. Injection molding, radio-frequency, or semi-automated pressure under hot-air will provide far greater consistency and reduced cost for higher volumes.
Complex & Miniature Catheter Tips
For very small and unique geometric features, it is not uncommon to require custom tooling and equipment from the start. Parts that are sub-micro sized (measuring just 0.1mm) will likely require injection molding. Such small features will require very low melt volume and controlled high speed and high-pressure injection to be formed and function properly.
The catheter may require very dissimilar materials unable able to bond by melt or adhesive. When joining these dissimilar materials, it may be required to use a transition layer in between the shaft and tip to ensure proper bonding or incorporate features that create a mechanical attachment of the materials.
Complex catheters will present more challenges as tips are required to perform more difficult functions such as deploying implants, delivering drugs, or drawing fluids. These tips will often have added complexities such as balloons on or near the tip, multiple lumen extrusions, radiopaque markers, side holes, and integrated elements such as temperature, pressure, or ultrasound sensors. Often, very thin wall thicknesses are required to meet the dimensional requirements of the device.
To properly compliment the catheter components, the extrusion may be required to dramatically vary the geometry and shape. It can become difficult to achieve the desired features (by design or assembly method) while still remaining within the geometric confines of the anatomy. Oftentimes, many of these applications become microscopic and require custom processing techniques to manufacture the desired design.
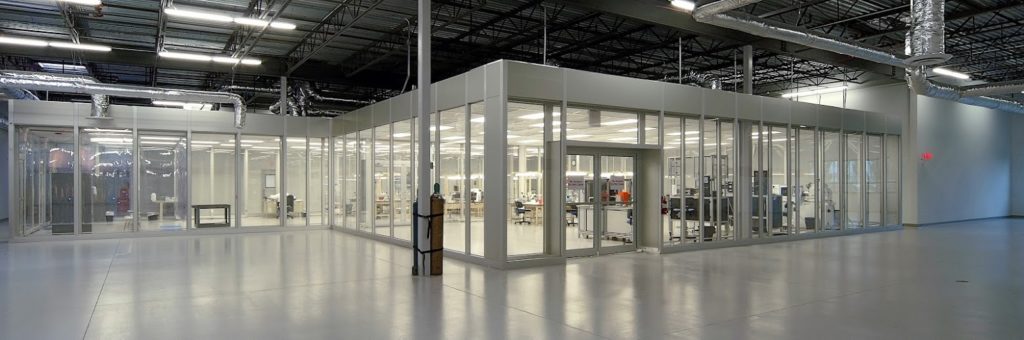
Medical Device Manufacturing
Careful consideration must be given to approaches in methods and their effect on ease of manufacture. With continued pressure on healthcare costs, and increasing competition for manufacturers, it is imperative that robust and sustainable processes are developed.
Tooling and equipment design are key factors in reducing cycle time and cost, while material selection and process control are crucial to the quality of finished goods. Die and-mandrel processes offer acceptable process control when implemented with semi-automated equipment that controls temperature, pressure, and time. Achieving consistent and predictable plastic flow is the challenge in maintaining output that meets requirements. High-pressure injection molding can achieve tip shapes that are not possible with die-and-mandrel methods and is an excellent approach when additional components such as markers must be embedded within the tip. In both methods, the reduction of secondary processes such as flash removal contributes to the ability to maintain low cost.
Choosing materials and refining a catheter tipping process can be challenging. When confronted with a more complex design, it is essential that proper material testing is performed throughout the design and development process to ensure the device maintains the acceptance criteria throughout. It is also imperative to work with a knowledgeable engineering team that is able to clearly identify what types of materials and processes will ensure a successful design.