It’s all in the tip when it comes to making catheters with state-of-the-art steerability and deflection.
By Andy Black & Tanner Hargens
Catheters often need to navigate tortuous anatomy with precise control of the catheter tip. Steerable catheters are often utilized for access into side branches from parent vessels to introduce guidewires and other devices into desired locations. The ability to steer a catheter is generally measured by how well torque is transferred from the proximal end of the catheter to the distal end while the catheter retains the desired shape.
Sufficient “steerability” can be achieved by reinforcing the catheter shaft with braided wire to enhance torque transmission and provide kink resistance. A common steerable catheter is constructed by braiding wire over a lubricious liner, which serves as the working channel, followed by melting and compressing an outer layer of thermoplastic onto the braided liner to create a single fused composite.
Many steerable catheters have a preset shape at the distal tip. These preset tip shapes can be manipulated with guidewires and shaft rotation for access to challenging anatomy. There are a large variety of preset tip shapes including a slight angle, cobra, visceral, pigtail, etc.
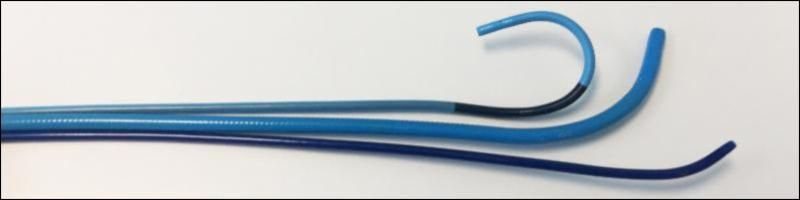
Deflectable catheters
Some catheters may be required to place the catheter tip very precisely for a prolonged period at body temperature. Examples include guiding catheters, endoscopy, imaging catheters and tissue ablation. For these more challenging needs, deflecting the tip into a defined curve can control the catheter tip location.
One of the most common ways to deflect the tip of a catheter is by pulling a wire that runs the length of the catheter shaft and anchors itself within the distal tip of the catheter. This type of deflectable catheter design usually has a relatively stiff proximal shaft and a softer distal tip, allowing the distal tip to deflect when the wire is pulled. Using various durometers of the thermoplastic outer layer, melted onto the braided liner, commonly alters the shaft stiffness.
Deflectable catheters incorporate a dedicated liner running the entire length of the catheter, to allow the pull wire to move freely between the soft distal tip and the stiffer proximal shaft segments when they are all joined together. The pull wire is typically anchored by welding the wire to a ring and then embedding the ring within the distal end of the catheter. The location of the embedded ring will dictate the deflected shape when the wire is pulled from the proximal end.
For catheters that need to deflect in two directions, two pull wires will be used. Separate liners will be dedicated to each pull wire, and the wires will typically be welded to the ring embedded in the tip 180° relative to each other. These pull wires can be connected to a levered bell-crank mechanism in the handle for simple and smooth control of the tip with two directions of deflection.
Advanced design considerations
There’s an increasing need for more advanced design and material considerations to alter the steerability and deflection of the catheter. For example, structural heart implant delivery systems must navigate a tortuous path and then maintain the intended shape while a relatively large, rigid implant is advanced through the catheter.
These more advanced catheter systems often require varying degrees of deflection, such as slight deflection in one segment with a very tight deflection curve in another segment. Straight lengths of catheter shaft between these deflection segments can also be utilized to create “reach” for optimal tip location when deploying other devices through the catheter.
Multiple deflection zones can be integrated into the length of the catheter by varying the outer layer materials, the shaft reinforcement, and/or the pull wire anchor locations. Varying the outer layer materials typically involves changing the durometer of the material. The shaft reinforcement may be altered by changing the braid pattern, transitioning from braid to coil, or encapsulating a laser-cut hypotube. The pull wires can be anchored at different locations along the length of the catheter or be radially offset when welded to the same anchor ring.
All of the options above can be combined for a near limitless variety of desired results. Assembly of catheters that combine these features can require a surprisingly amount of subtle finesse.
Emerging technologies
New methods of catheter navigation are emerging. Rather than utilizing a pull wire, force can be transmitted to the distal tip using concentric tubes or small hydraulic chambers positioned within the tip of the catheter. Force can be generated within the tip by electric or thermal energy. Magnets can also be integrated into the tip and then controlled by external magnetic systems. Any one of these new technologies may ultimately displace the current methods of steerable and deflectable catheters.
Andy Black heads all product development from initial concept to manufacturing and leads project teams at Medical Murray’s four facilities nationwide.
Tanner Hargens has extensive expertise in device design and commercialization and directs the sales engineering team at Medical Murray (North Barrington, Ill.).