Using a bioabsorbable polymer in your medical device can allow surgical patients to heal without needing a second surgery to remove the device. These devices often lead to better surgical outcomes and lower treatment costs. Some devices with bioabsorbable polymers we have developed & manufactured include:
- Vascular closure and repair devices
- Absorbable stents & braid, both components and subassemblies
- Fasteners, anchors, & screws and their delivery systems
- Tympanostomy tubes (Ear tubes)
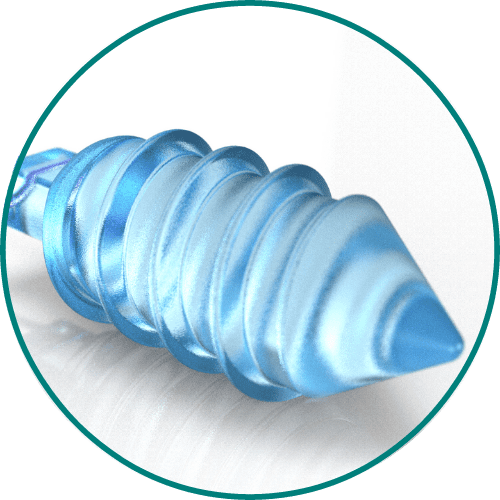
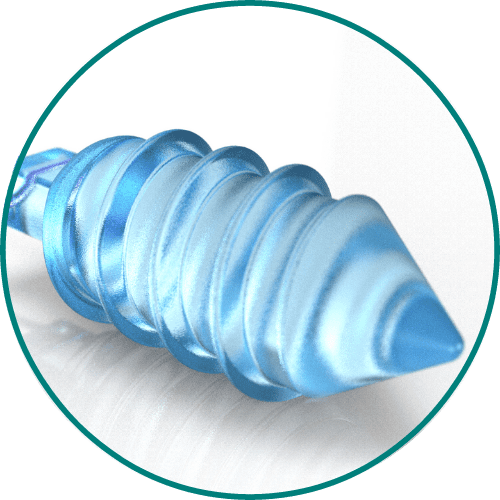
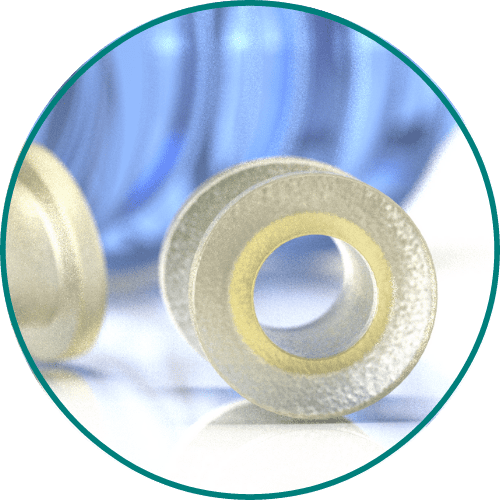
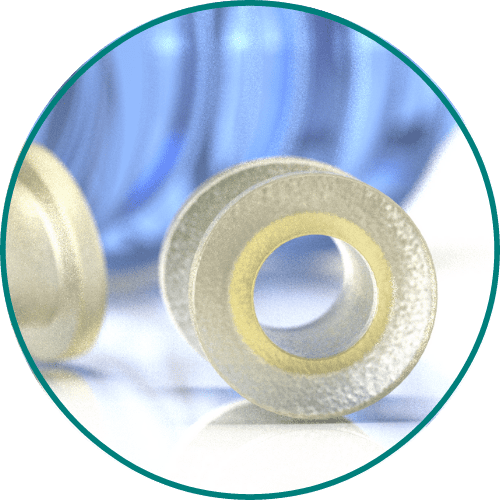


Medical Murray can tailor the composition of the specific bioabsorbable monomers or polymers for your device to meet specific requirements for absorption speed, tensile strength, stiffness, or toughness. We have experience processing and handling the following bioabsorbable polymers:
PGA (Poly-glycolide) | PLA (Poly-lactide) |
PLGA (Poly-lactic-co-glycolic acid) | PDO (Poly-diaxanone) |
TMC (Trimethylene carbonate) | PCL (Poly-caprolactone) |
PGA (Poly-glycolide) | PLA (Poly-lactide) |
PLGA (Poly-lactic-co-glycolic acid) | PDO (Poly-diaxanone) |
TMC (Trimethylene carbonate) | PCL (Poly-caprolactone) |
If you would like to learn more about Medical Murray's experience with Bioabsorbable polymers, check out our articles on the Molding of Bioabsorbable Polymers or Injection Molding Complex Bioabsorbable Implants.
Bioabsorbable Processing, Handling, and Packaging
Bioabsorbable polymers require special handling procedures from resin to finished device and packaging.
Inventory Storage: Bioabsorbable / absorbable polymers are typically kept in moisture-free containers and cold storage to preserve their longevity.
Process Sensitivity: Bioabsorbable polymers are typically dried before processing. Molding these polymers using a low melted volume, controlled speed, and short sprues allows us to mold micro parts and features without causing excessive polymers degradation.
Assembly Handling: Limiting moisture during all steps of the manufacturing process is essential for Bioabsorbable polymers. Our ISO 13485:2016 certified cleanroom is continuously monitored for humidity fluctuation, and viscometers & moisture titration monitors are used to test for material degradation during processing and assembly.
Finished Packaging: Bioabsorbable devices can be packaged in pouches purged of residual Oxygen and back-filled with Nitrogen, along with desiccant chips. This preserves the device's shelf life and slows degradation due to exposure.
Bioabsorbable polymers require special handling procedures from resin to finished device and packaging.
Inventory Storage: Bioabsorbable / absorbable polymers are typically kept in moisture-free containers and cold storage to preserve their longevity.
Process Sensitivity: Bioabsorbable polymers are typically dried before processing. Molding these polymers using a low melted volume, controlled speed, and short sprues allows us to mold micro parts and features without causing excessive polymers degradation.
Assembly Handling: Limiting moisture during all steps of the manufacturing process is essential for Bioabsorbable polymers. Our ISO 13485:2016 certified cleanroom is continuously monitored for humidity fluctuation, and viscometers & moisture titration monitors are used to test for material degradation during processing and assembly.
Finished Packaging: Bioabsorbable devices can be packaged in pouches purged of residual Oxygen and back-filled with Nitrogen, along with desiccant chips. This preserves the device's shelf life and slows degradation due to exposure.