Braiding is a cornerstone of many interventional medical devices, including catheters, stents, guidewires, and biomedical structures. At Medical Murray, we use a variety of braiding methods to help our clients achieve optimal device performance. From basic braided tubing designs to advanced, customized braids with back-braided ends that minimize tissue trauma, braiding can enhance flexibility, kink resistance, torque transmission, and more. Below, we’ll walk through braiding fundamentals and touch on more advanced techniques relevant to high-density metallic, polymeric, and bioabsorbable constructs.
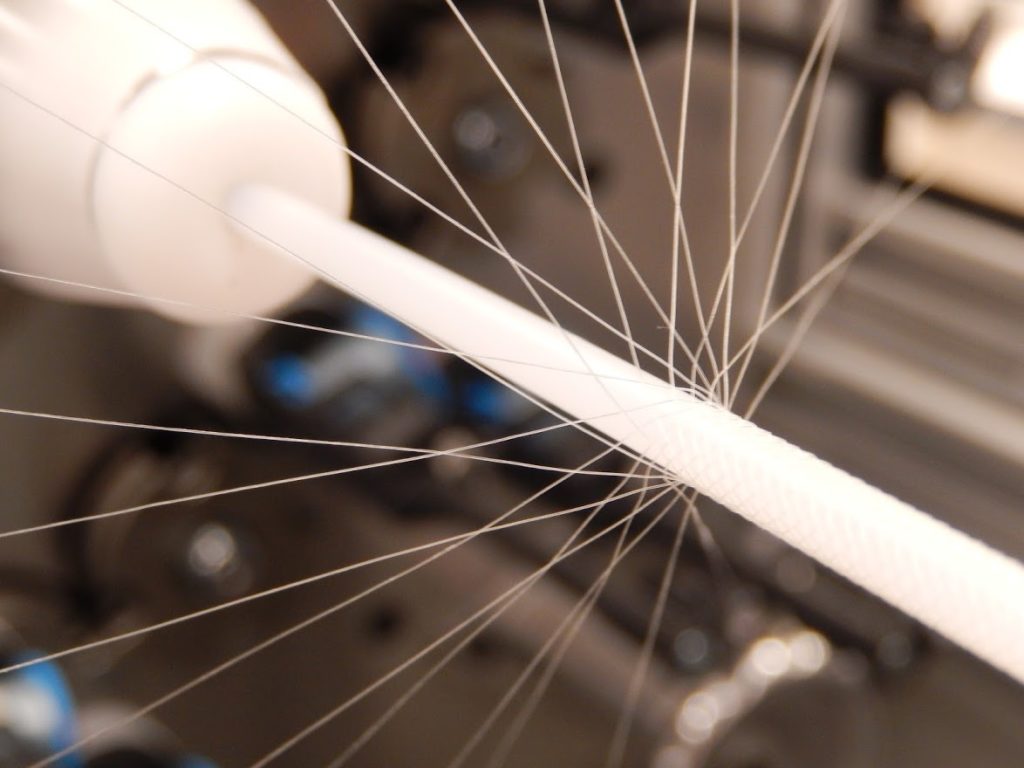
Braiding Fundamentals
Braiding involves weaving metal or polymer filaments (e.g., stainless steel, nitinol, PET, PEEK) around a mandrel to create structures with tailored strength and flexibility. Changing variables like filament diameter, braid angle, and pick count (crossovers per unit length) lets us dial in the exact performance needed. For instance, stents rely on braided frameworks for radial support and vessel conformity, while catheters often have braid-reinforced tubing to enhance pushability and torque response.
Patterns range from simple 1-over-1/1-under-1 braids to more complex designs that adjust density along the length of the device. Braid patterns can be as simple as a single weaved layer or more complex multi-layer designs with varying densities. Tweaking these patterns can dramatically change a device’s rigidity or flexibility. Hand braiding can also be used for prototyping or for sections requiring a precise, artisanal approach.
Stents, Implantable Structures, and Reinforced Tubing
Stents often rely on braided metal or polymer structures to balance radial strength with vessel conformity. Braiding brings together radial strength and flexibility while keeping the overall profile low. By combining implantable substructures with coverings, coatings, or laser-cut elements, manufacturers can further refine device performance.
Braid-reinforced tubing is a mainstay for catheters, offering precise control during navigation and deployment. It addresses kink resistance to ensure smooth trackability through tortuous anatomy, torque transmission to facilitate controlled rotation, and pushability to improve device steering and positioning.
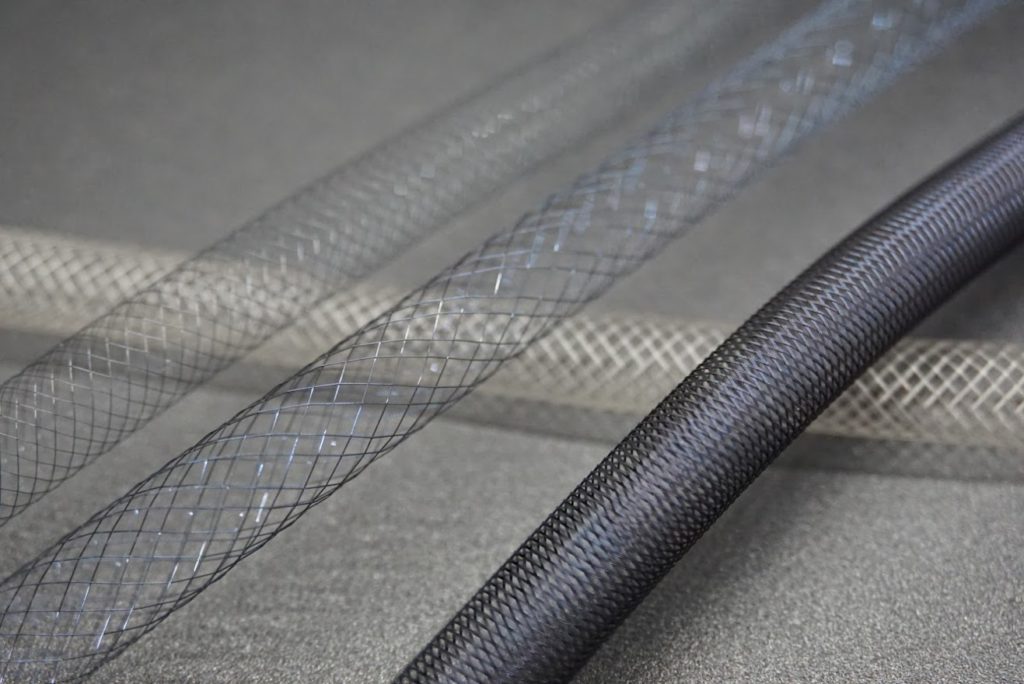
Braiding versus Coiling
Both braiding and coiling serve as reinforcement mechanisms for catheters and other tubular devices. The choice often depends on how much torque response, stiffness, or kink resistance your design needs. Coiling can offer localized support, advanced flexibility, more linear responsiveness, or a thinner wall and smaller diameter, which can be critical for neurovascular or microcatheter applications. At Medical Murray, we offer braiding, coiling, and a hybrid approach, where we combine braiding and coiling to optimize distinct sections within the same catheter.
Advanced Braiding Techniques
Medical Murray specializes in braiding for devices that demand superior radial strength and kink resistance. Higher pick counts and refined tension control enable more robust, uniform braids.
Back-braiding is a specialized technique allowing for smooth, closed ends. This is ideal for some stents, occlusion devices, and catheter tips. These atraumatic ends minimize tissue damage and reduce friction during delivery. Medical Murray’s process ensures consistent, secure back-braided terminations to improve safety and patient comfort.
Bioabsorbable braids, using materials such as polylactic acid (PLA) or other resorbable polymers, provide temporary structural support. Over time, the braid is absorbed, reducing the risk of chronic implant complications (Poly-Med, 2023). This technology is increasingly applied to scaffold devices and drug-eluting implants.
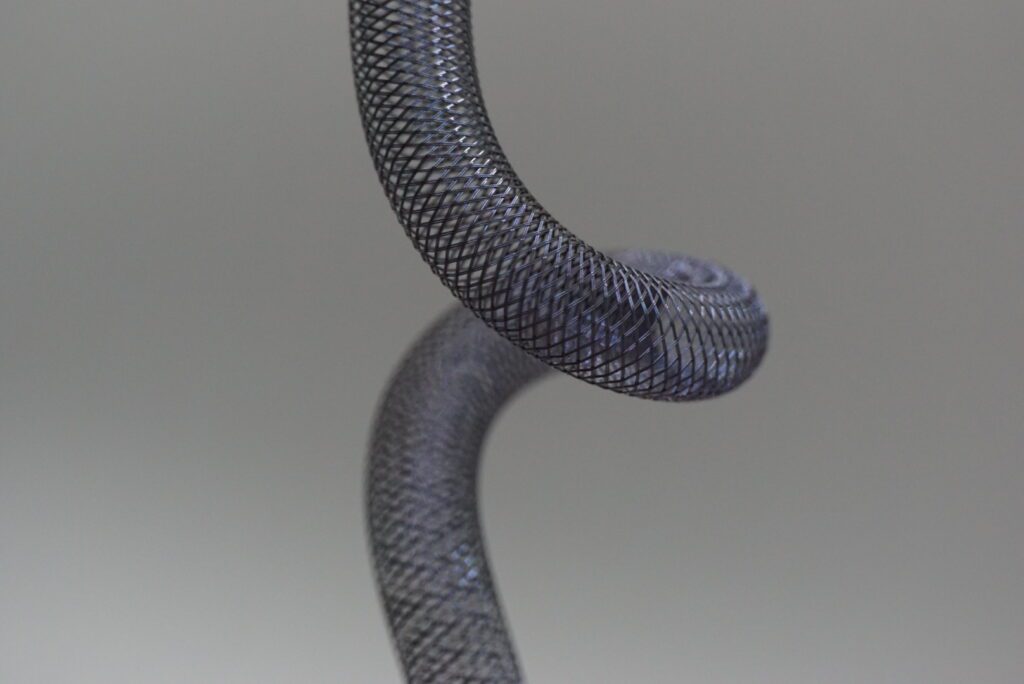
Braiding remains essential for interventional medical devices, offering control over mechanical and structural properties, promoting device longevity, and improving patient outcomes. Leveraging braiding versus coiling, or a hybrid approach, depends on the unique demands of each clinical application. At Medical Murray, we combine decades of braiding expertise with flexible manufacturing capabilities to deliver high-performance catheter shafts, stents, and other implantable devices, including advanced back-braided ends for atraumatic deployment and more sophisticated constructs. Reach out and explore how braiding (or coiling, or both!) might fit your next development project!