Why Bioresorbable Implants Matter
Bioresorbable implants—made from polymers that gradually dissolve in the body—are transforming the medical device landscape. They serve their purpose during healing, then safely break down into byproducts the body can metabolize. By doing so, they eliminate the need for removal surgery and reduce the risk of complications often associated with permanent implants.
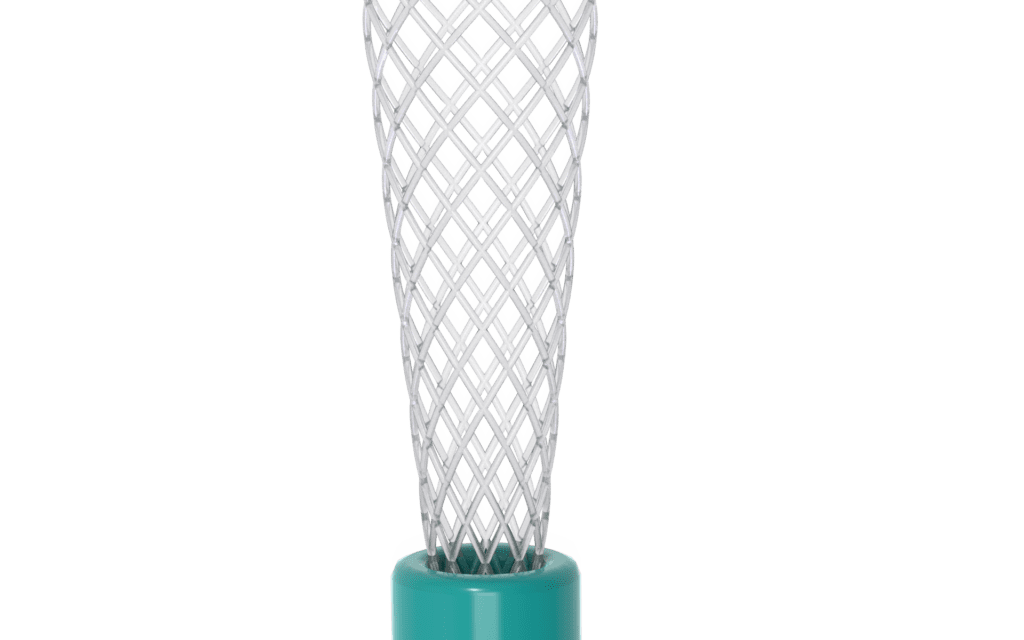
The Science Behind Bioresorbable Polymers
Commonly used bioresorbable polymers include polylactic acid (PLA), polyglycolic acid (PGA), and poly(lactic-co-glycolic) acid (PLGA). These materials degrade through hydrolysis, producing lactic acid and glycolic acid—substances the body already knows how to process. A key challenge is matching each polymer’s mechanical strength with the ideal degradation rate for the clinical application. On top of that, manufacturing methods such as extrusion and injection molding must preserve the polymer’s chemical integrity—making control over temperatures and molecular weight distributions essential.
Controlling Exposure to Moisture
One often overlooked yet critical factor is limiting exposure to water vapor throughout manufacturing and packaging. Even low levels of moisture can prematurely start the degradation process and compromise both strength and shelf life. For that reason, these devices are ideally manufactured in a humidity-controlled clean room, ensuring that ambient moisture doesn’t accelerate breakdown before implantation. It’s also essential to remove all excess moisture from the final packaging to protect the device after it leaves the manufacturing floor.
At Medical Murray, our humidity-controlled class 7 clean rooms provide the level of environmental management necessary to keep devices stable during production. We also commonly include desiccants in the packaging to absorb any residual moisture, and we do a nitrogen purge of the packaging before sealing. This purge effectively replaces oxygen and moisture-laden air with dry nitrogen, creating the ideal environment inside the pouch and helping maximize the shelf life of each device.
Designing for Targeted Support and Timely Resorption
From an engineering standpoint, a bioresorbable implant must be robust enough to support tissues during the early stages of healing but not remain in place after its job is done. For instance, carefully selecting a blend of PLA and PGA can calibrate how fast the device will break down once implanted. Surface modifications and sterilization processes also play a role in performance and safety, helping ensure that the polymer remains stable and biocompatible during its functional lifespan.
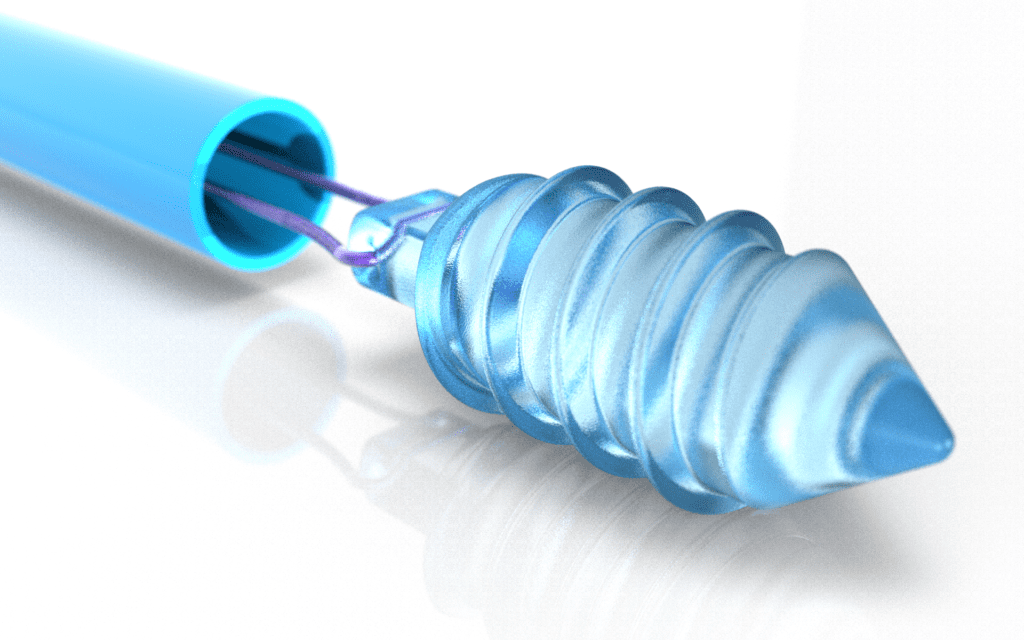
Applications Across Multiple Disciplines
Bioresorbable implants have been making waves in orthopedics, cardiovascular care, and soft tissue repair, among other areas. Orthopedic screws and plates can stabilize fractures and then degrade as the bone heals, removing the need for a second procedure. Bioresorbable stents help keep blood vessels and non-vascular tubes open when needed, then gradually dissolve to reduce complications.
Devices such as suture anchors can secure ligaments and tendons without leaving permanent material behind, lowering the risk of inflammation or rejection. Resorbable polymers can be formed into scaffolds for wound healing, allowing tissue to grow into and replace the scaffold before it fully degrades. This approach can reduce scarring and facilitate more natural regeneration. Bioresorbable implants can also be loaded with pharmaceutical agents and designed to release these drugs at a controlled rate. Over time, the polymer breaks down, ensuring a steady and targeted delivery of medication while avoiding the need for additional procedures.
Medical Murray’s Role as an Industry Leader
Medical Murray offers a unique blend of expertise, from selecting ideal polymer formulations to producing complex geometries using extrusion and injection molding. Our on-site testing capabilities verify mechanical properties, degradation rates, and biocompatibility, ensuring the finished product meets strict safety and performance requirements. By maintaining humidity-controlled clean rooms and using best-in-class packaging methods—complete with desiccants, nitrogen purging, and header pouches—we help safeguard the device’s integrity and extend its shelf life. Our end-to-end regulatory support further streamlines the journey from concept to commercialization for our clients.
Looking Ahead
Bioresorbable implants continue to reshape patient care by eliminating hardware removal surgeries and decreasing long-term complications. When combined with prudent material selection, rigorous design, meticulous moisture control, and reliable manufacturing practices, these polymers can offer targeted healing support and then gracefully exit the scene. Thanks to our robust capabilities in both medical device engineering and manufacturing, Medical Murray remains at the forefront of this promising field—ready to develop next-generation devices that benefit patients and healthcare providers alike. Contact us today to learn more about how we can support your project.