The medical device design and development process is complex and time-consuming. It demands a wide range of expertise in engineering, regulatory compliance, and clinical testing. However, there are several strategies that companies can use to bring safe and effective products to market more quickly.
Know the Needs Your Medical Device Serves

It’s critical to clearly understand the clinical needs that are not being addressed by the current treatment options along with the value proposition and business case for the new medical device. Getting feedback from end-users and hospitals using early prototypes will identify potential issues and areas for improvement when it is cheaper and faster to make changes. Forecasted manufacturing quantities and viable cost of goods targets should inform design and material selections from the beginning of product development to reduce late-stage redesign work and speed up your time to market.
Once you are confident that the new medical device concept is viable, categorize product features as “must-have” or “nice-to-have”. The first generation of the device to be commercialized will have all the must-have items while subsequent generations of the medical device may integrate the nice-to-have items that are too challenging or costly for the first generation. This type of product evolution plan can help prevent scope creep so that the first-generation device achieves development goals as soon as possible with the least amount of investment, paving the way for the development and launch of subsequent generations.
Rapid Learning from Rapid Prototypes (or Simulation)
To develop single-use devices, it is often best to produce rapid, cost-effective prototypes early and often, subjecting those prototypes to bench testing to help define the design requirements. These prototypes may be partial builds focused only on the most difficult design requirements that need the most attention. Early bench testing can also refine test methods to be used later for design verification.
Don’t customize components and features unless it’s necessary; instead, take advantage of existing technologies and platforms. This can be done by building upon existing products and designs or by incorporating off-the shelf components and systems into new devices. This will reduce the amount of time and cost required to develop new products and can also ensure that the devices are safe and effective.
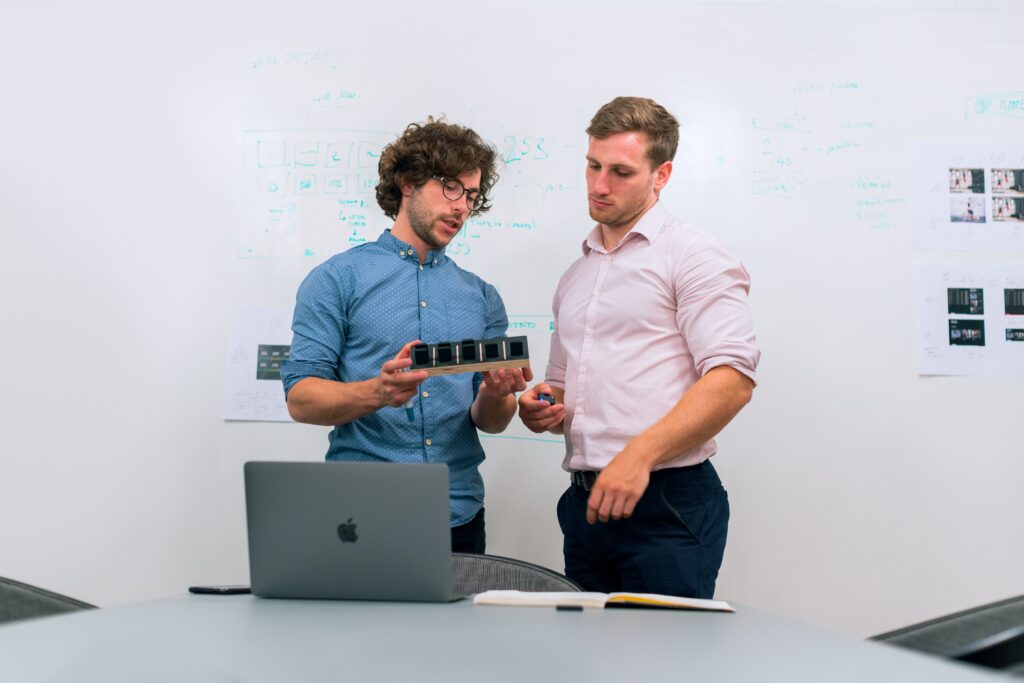
When custom components and features are needed, rely on rapid, additive manufacturing processes like 3D printing or selective laser sintering whenever possible. What used to take weeks and thousands of dollars to machine or mold parts can now be produced overnight for a relatively low investment. Additive manufacturing may not always be viable for the commercial product, but we recommend using these processes for form factor models and fit-check prototypes. Often, these additive manufacturing methods can continue to be used throughout preclinical testing up until design verification testing.
For development of implants that have a mechanical function, a lot of time and money can be saved by investing in advanced design and simulation tools. These simulation tools can be used to quickly and accurately model and test new designs, which can help to identify and address potential issues early in the development process. This can help to reduce the need for expensive and time-consuming physical testing and prototyping.
Communicate with Regulatory Agencies
Another important strategy is to establish a strong partnership with regulatory agencies. This can help to ensure that the device development process follows all relevant regulations and can also help to expedite the approval process. Medical device development companies can work with regulatory agencies to establish clear and consistent guidelines and can also provide early feedback on their designs to identify and address any potential issues.
Extend Your Team
Consultants and contract development companies have been used to accelerate medical device development for decades. These subject matter experts should review the design, test results and project plan repeatedly to identify risks, contingencies and possible faster routes. Timely expertise may be the greatest way to accelerate development and prevent foreseeable setbacks.

Finally, companies can either invest in advanced s equipment and learn new processes or partner with a contract manufacturer. Either path will help improve the speed, efficiency, and quality of manufacturing, which can help to reduce the time and costs associated with bringing new devices to market. Working with a contract manufacturer of medical devices can have numerous benefits for companies that develop and market medical devices. A contract manufacturer can save companies time and resources, provide access to specialized expertise and equipment, and help to reduce the risk associated with product development and manufacturing. This makes them a valuable partner for medical device companies of all sizes.
By Tanner Hargens